CNC Routers: Five tips for getting the best cut
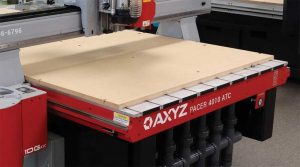
5. Keep a maintenance schedule
An important part of creating a cutting strategy is to ensure regular maintenance checks are conducted on one’s CNC router equipment. By keeping a maintenance log, following a schedule, and sticking to it, signmakers can ensure trouble-free operation. The following inspection checks should be reviewed as a way to extend the life of a CNC router and tools for many years to come.
- Clean it regularly. Any buildup of fluids or chips can easily get into the bearings and controls—this can be a sure recipe for problems if not corrected every day.
- Change filters. Although there is no standardized schedule (it depends on the specific machine), all filters should be checked weekly and changed as needed.
- Lubricate. The nice thing about routers is that despite all their parts, they do not require extensive lubrication. Bearings, pumps, and oscillating knives need regular lubrication, but this will vary from one machine to the next.
- Air supply cleaning. Most CNC routers operate with pneumatic air that has to be clean, dry, and maintained at a steady pressure (more than 80 pounds per square inch [psi] or 6 barometric). Damage to the machine is likely in a very short time frame due to incorrect specifications; therefore, pressure should be checked regularly.
- A safe and proper power supply. The power must be sufficient and safely connected as required by local utility regulations. Machine failure is likely to occur in cases of poor electrical grounding, low voltage, or insufficient capacity. As is the case with every computer-operated mechanism, power spikes will cause serious damage.
Common issues
For those signmakers who are still not getting the results they expect, the following are some common causes to check:
- Over-tightened collet;
- Incorrect feed rate (finishing pass);
- Incorrect spindle speed (finishing pass);
- Wrong type of material (extruded not cast); and
- Wrong cutter.
Following these tips can help one optimize their routing experience and keep their machine working at high capacity for many years to come. There is a wealth of knowledge out there to tap into; therefore, signmakers should take the time to partner with an experienced CNC machine supplier. Selecting the right tools, materials, and options makes a world of difference—especially when turning an ordinary project into an innovative product that will make one’s business stand out from the competition.
Susan Mattine is the communications and public relations associate for AXYZ Automation Group, a global leading manufacturer of tailored cutting solutions. She can be reached via email at smattine@axyz.com. For more information, visit www.axyz.com.