Wide-format Printing: Optimizing colour management
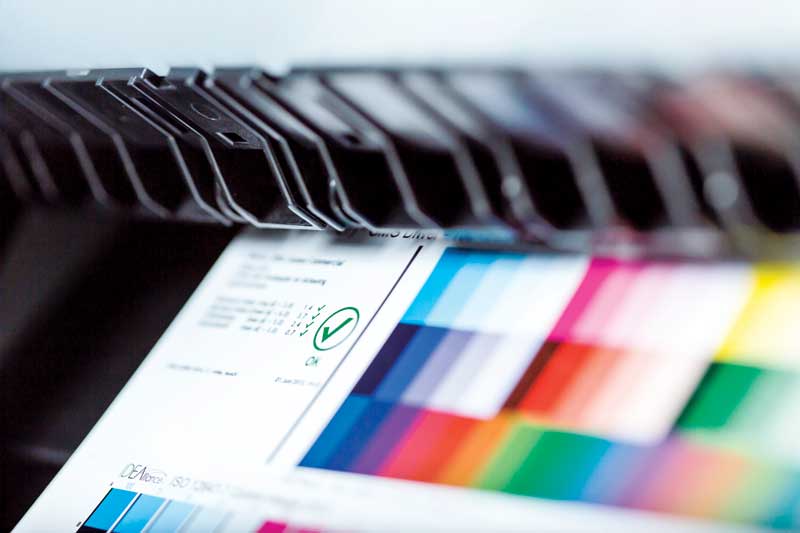
Standardizing printing
The goal of standardized printing is to reduce the colour deviations and variations in graphics produced by different devices. These differences usually exist because machines vary in their colour capabilities—sometimes quite dramatically—due to a variety of printhead technologies, ink formulations and substrates.
Standardized printing also respects the designer’s intentional (or unintentional) overprint, transparency and blend effects by converting colours correctly to a standard before the conversion to the printer’s own colour space. This approach ensures the output is accurate and uses everything the printer’s gamut has to offer. As there is no need to test the printer to see if the job will be handled correctly, this saves time for the operator who is preparing and printing the job.
The way to standardize printing is to convert all incoming colour spaces—whether CMYK or not—to a chosen reference profile first, like GRACoL, and only thereafter to the printer profile. Thus, all of the colours are first matched to a standard, then converted with the printer’s specific capabilities in mind, which helps maintain overall colour appearance between different devices.
A subset of the International Organization for Standardization’s (ISO’s) Portable Document Format (PDF) specification known as PDF/X was developed for this reason, among others. PDF/X files contain the reference output intent with which they should be processed, so as to deliver a single job with everything embedded. In any PDF/X3 file (or a more recent version), all of the elements that do not match the output intent’s colour space must be tagged with ICC profiles to ensure correct colour conversions.
This file format is now broadly supported by mainstream software applications, including Adobe Illustrator and InDesign, making it very easy to specify how a sign shop’s customers should supply their jobs in the first place. They can also be pre-flighted very easily to ensure they are acceptable before printing. The files should be exported to the most recent version of PDF/X available.
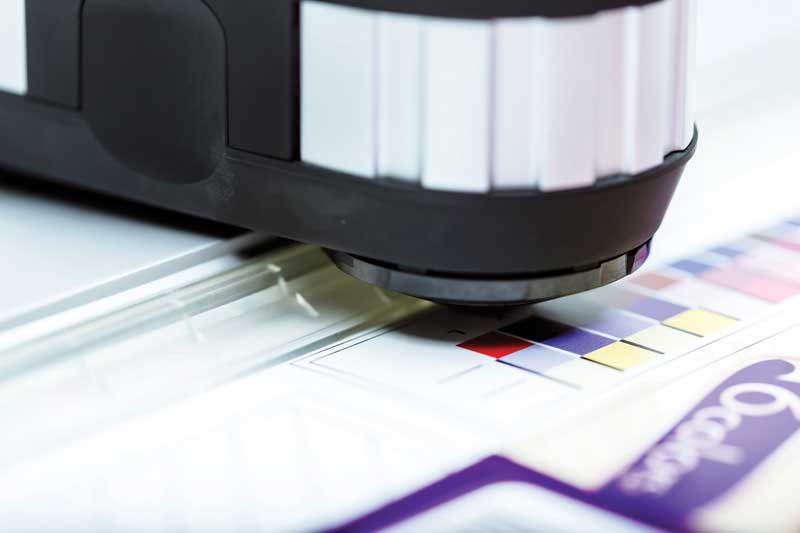
This approach to standardizing converts all elements to a single colour space by way of reference profile and supports spot colours. The use of device-link profiles becomes unambiguous, as there is only one colour space after the process of standardization.
Indeed, the use of device-link profiles is far superior to typical ICC conversions. By allowing a workflow to calculate a direct link, it delivers the following advantages:
Neutral grey
When the reference space is fully known, so too is the grey axis, for which the device-link profile can then be optimized.
Ink savings
Device-link profiles can maintain detailed midtones and shadows while saving significant quantities of ink. In addition to reducing overall costs, this extends the longevity of printheads, improves printability on various types of media and saves energy by enabling printing at lower temperatures.
Repeatability
The device-link profile contains information about which colour targets it needs to hit and how to direct a specific printer to return an image to its original state.
In practice, this means when a printer’s colours start to ‘drift,’ a simple print-and-measure process—with a relatively small colour target, involving approximately 500 patches for a CMYK printer, read with a spectrophotometer—can compensate. This means the printer will produce the same output result, day after day, without much external effort.