Wide-format Printing: Effective process control with G7-based calibration
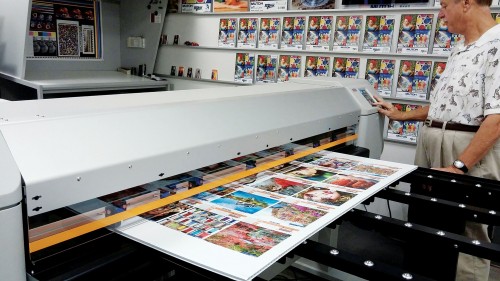
By Christopher Brown
Process control is critically important to efficient manufacturing, regardless of the product being made. Maintaining consistency day-to-day is virtually impossible without tight control over the manufacturing process. Wide-format printing is no different, as it takes raw materials—including inks, media and laminates—and creates a more valuable end product, such as a banner, sign or wrap.
By integrating straightforward process checks and controls into the wide-format print production workflow, it becomes possible to ensure more consistent and predictable results, curb waste and reduce overhead costs. The key is to establish ‘pass/fail’ criteria based on known conditions to which each printer can be calibrated. Then, after implementing control checks during production, data should be archived to help isolate variations and determine their causes over time.
Establishing reliable conditions
For many signmakers, colour management is a process of measuring targets and using software to develop International Color Consortium (ICC) profiles, which involves generating a model of how a printer recreates colours under specific given conditions. Should the future performance of that printer change, however, due to environmental variations, mechanical wear, different inks or media or maintenance issues, then the validity of a profile and, thus, the accuracy of the colour can fall into question.
As mentioned, the goal of process control is to establish known conditions for the printer—before generating the ICC profile—that can be reliably recalibrated should any change cause colour drift. This control will maintain the accuracy of profiles throughout the production run.
In 2006, the not-for-profit International Digital Enterprise Alliance (IDEAlliance)—previously known as the Graphic Communications Association (GCA)—developed the G7 methodology for calibrating inkjet printers and other cyan, magenta, yellow and key/black (CMYK) output devices to a common set of ‘aim points’ to produce graphics with a common visual appearance. Since then, G7 has also become an American National Standards Institute (ANSI) specification and several G7-based software options have become available, in both stand-alone and system-integrated configurations.
G7 is not colour management per se, but does avoid subjective and often ambiguous definitions of good visual reproduction, replacing them with objective targets based on the colorimetric relationship of neutral points between white and black. The results are referred to as neutral print density curves (NPDCs).
One key aspect of G7 calibration is taking the colour of the substrate into consideration when building an NPDC. If the substrate has a yellow cast, for example, then the same amount of yellow is removed from the corresponding NPDC, thereby removing the influence the substrate’s yellow would have on a print. This explains, in part, how G7 calibrates all devices to a common visual appearance, regardless of colour gamut.
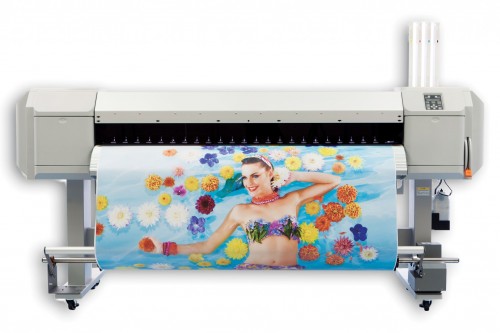
The science behind the standard
The science behind G7 goes back nearly a century to some of the earliest experiments researching how a person with normal vision—referred to as the standard observer—interprets colour. One important discovery was a particular human sensitivity to grey balance; that is, people perceive colours relative to a neutral stimulus. They may not know if particular colour is correct without a visual point of reference, but they will recognize if an mage possesses a colour cast, even a subtle one.
From the earliest days of colour film photography, calibrating the exposure of red, green and blue (RGB) plates to make a print was accomplished by calibrating to a standard neutral density. The G7 methodology, though new, is based on the same photographic processes.
An alternative to linearization
In most cases, for inkjet printing applications, G7 calibration can replace linearization and avoid the need for an additional step in the colour workflow. Rather than linearizing a printer in the conventional way, which calibrates the device only to itself, G7 calibrates a printer to a set of independent targets derived from white and black points, as mentioned, that are unique to the printer, inks and media. Compared to linearization, the process requires no more time or expertise. And the resulting NPDCs can be applied in the same way as conventional linearization curves.
Primary ink limits may still be applied, depending on the printer and substrate, but secondary ink limits are generally unnecessary. In some cases, depending on the raster image processor (RIP) configuration, the calibration curves can be imported directly into the RIP software in lieu of linearization curves. In other cases, the linearization curves are kept null and the calibration curves are applied inside the ICC profile. Either way, if colour drift should begin to occur, then the calibration curves may simply be reiterated and reapplied, which in most situations will prevent the need to regenerate the ICC profile.
Linearization calibrates only to transient conditions that can change over time, with no good way to ensure colour reproduction is consistent and repeatable; whereas G7 establishes conditions against which any printer can be tested for conformity.