Screenprinting: Stirring up passion and precision
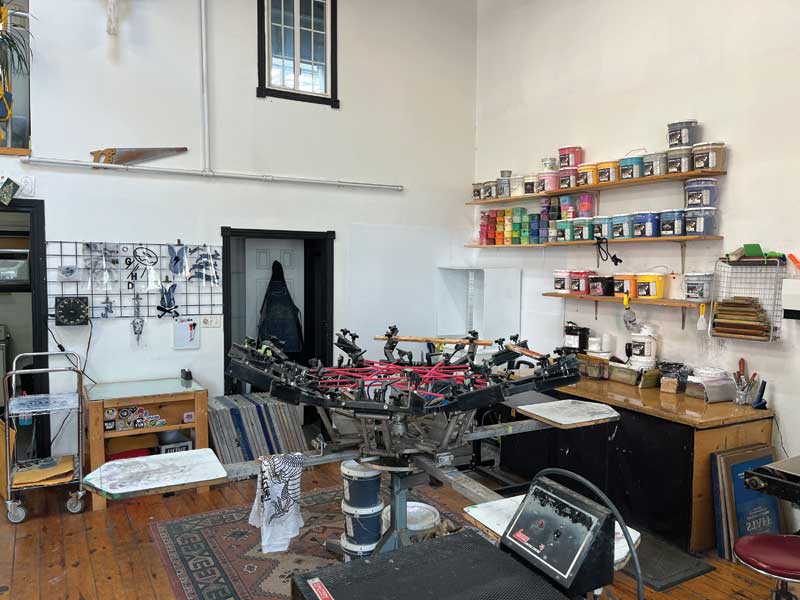
From a roller derby start to a thriving screenprinting enterprise, Caitlin Watson has been a key player in Toronto’s print scene for years. Now, as the owner of the city’s only female-operated print shop, Sugarbomb, Watson and her team specialize in quick turnarounds and high-quality, hand-printed products. They pride themselves on giving each order meticulous attention and truly loving what they do.
In an interview with Sign Media Canada, Watson shares insights into the inspiration behind Sugarbomb, their hands-on quality processes, challenges faced, memorable projects, durability measures, and tips for beginners.
Sign Media Canada (SMC): What inspired you to start a screenprinting business?
Caitlin Watson (CW): We began as a roller derby-focused business, specializing in adding names and numbers to sports jerseys. This evolved into producing full jerseys with team logos on the front, leading us to pivot into screenprinting. Over time, we invested in new equipment and upgraded our studio. I’ve always been interested in print. This passion for print, coupled with a fashion design degree where my final project involved self-printed fabrics, which I screenprinted myself, guided this transition. I’m a self-taught screenprinter, with many people around me who have been in the industry and helped me immensely along the way. My right-hand woman, Stacey, brings invaluable experience from various screenprinting shops.
SMC: How do you ensure the quality and consistency of your prints?
CW: As a fully manual screenprinting business, we print and process everything by hand. This means many eyes and hands are involved in every step, as nothing is automated. We can spot mistakes or blockages in the screen as they happen and address issues immediately. This hands-on approach ensures high consistency and attention to detail.
SMC: What challenges have you faced in the screenprinting industry, and how have you overcome them?
CW: As a female-owned and operated business, we occasionally face challenges with trust, especially in a traditionally male-dominated industry. Sometimes we encounter people who don’t entirely believe we know what we’re doing. This is changing now. Moreover, with more than 25 years of combined experience between Stacey and me, our work and product speak for themselves.
SMC: Can you tell us about a memorable or unique project you’ve worked on?
CW: We love working for artists. We also love working for the queer community. We feel fortunate to have so many talented artists as clients. It’s always exciting and fun when bands come to us just as they are about to go on tour, and we get to print a whole load of their merchandise. It also gives us great joy when we print for small businesses, coffee shops, and clothing stores. We truly enjoy collaborating with small businesses and find it a pleasure to work together.
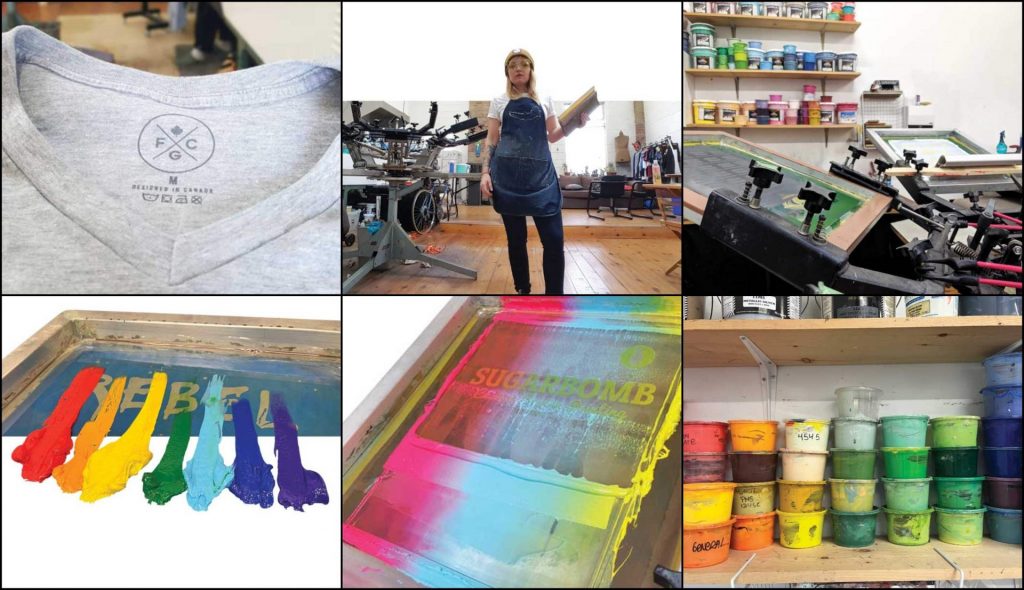
SMC: What measures do you take to ensure the durability and longevity of your screenprinted products?
CW: We use a heat thermometer gun to ensure the plastisol reaches the correct temperature during curing. Additionally, there is a stretch test which confirms the ink is fully cured on the garment. This process guarantees a durable and high-quality print. Plastisol is known for its longevity—band shirts from the ‘70s with holes in the garment are a good testament to just how long-lasting they can be because they outlast the shirt itself. When properly cured, plastisol prints last a very long time.
SMC: What are the most common mistakes beginners make in screenprinting, and how can they be avoided?
CW: Screenprinting at home can be time-consuming. When I started, I worked in my bathroom or living room, and I was always surprised by how long it took. You need to coat the screen, wait for the emulsion to dry, burn the screen, wait for it to dry again, and then set up the job. Doing just one project at a time involves a lot of waiting for things to dry. I recommend setting aside a few days to complete a project if you’re short on time.
There are also many techniques involved, such as the angle for holding a squeegee and getting used to plastisol ink. With water-based inks, you must be cautious of their quick drying time, which can clog the screen if you’re not properly flooding the screen before you do the next print. Learning these basic techniques and tricks of the trade can make the process easier. While it takes time to master, screenprinting can be done inexpensively at home and is accessible to most people, making it a great medium to start playing with.