Making the Right Substrate Choice
By E. Tyler Reich
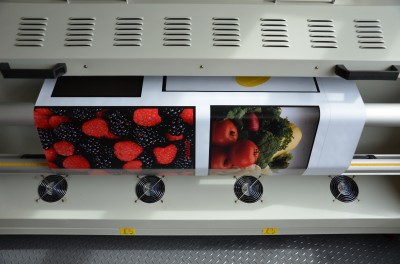
In today’s wide-format printing market, there is an expansive variety of choices when it comes to adhesive-backed vinyl, so it is understandable if signmakers—especially those new to the digital printing of graphics—are confused which specific materials are best-suited for the jobs they need to produce.
To address this confusion, it is best to go back to basics and group these vinyls into two main categories—calendered and cast—on the basis of their manufacturing processes. These two types can also be further broken down into four sub-categories based on their molecular composition.
Calendered
Calendered vinyl is produced by applying heat and pressure with a very smooth rolling device, i.e. a calender. The process is similar to flattening pizza dough with a rolling pin.
Naturally, when the vinyl molecules are stretched, just like the molecules of rolled pizza dough, they have a tendency to retract slightly over time. This effect is known as molecular migration.
When single molecules are used to form calendered vinyl, the material is known as ‘monomeric.’ The resulting molecular arrangement can be compared to using tiny building blocks to construct a large structure. It is very difficult when using tiny building blocks, however, to keep all of them in perfect order. External forces—including atmospheric effects, temperature changes, inks, chemicals and other foreign contaminants—can cause them to shift slightly, due to the unbonded spaces between the monomers. This can mean a high degree of molecular migration.
When the same large structure is built out of larger blocks, it is known as ‘polymeric.’ In this case, monomers are joined together using covalent bonds to form polymers.
As the larger polymers take up more volume than monomers, they reduce the unbonded space between molecules and, therefore, limit the ability of foreign contaminants to enter that space. This also allows the polymers to remain more firmly in place, with only a small degree of molecular migration.
What this means for wide-format graphics is monomeric calendered vinyl is more susceptible to shrinkage and atmospheric damage than polymeric calendered vinyl. Both types of materials can be printed with solvent-based, eco-solvent, ultraviolet-curable (UV-curable) and durable aqueous ‘latex’ inks, but monomeric vinyl is only recommended for indoor use up to one year or for temporary outdoor use (i.e. less than six months). Polymeric vinyl can withstand the shrinkage of molecular migration much better and its greater resistance to atmospheric damage makes it a better outdoor signage product. Indeed, it will usually last about three years outside before beginning to degrade.
The big advantage of using monomeric vinyl is its lower cost. And the quality is generally good enough; informal market studies show about 80 to 90 per cent of point-of-purchase (POP) display applications can be accomplished successfully using monomeric vinyl, because advertising content is changed out so frequently, with a promotional cycle of six months to a year at the maximum. There is no reason to waste money on an ‘overkill’ product instead.
Also, some vinyl manufacturers allow their monomeric calendered materials to settle into molecular migration before they sell them to sign shops. This is called pre-shrinking and helps less expensive monomeric vinyl perform similarly in the field to more expensive polymeric vinyl, at least with regard to shrinkage.
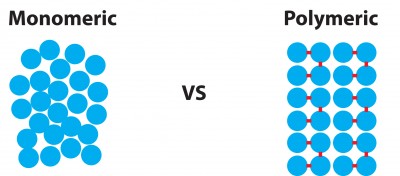
Cast
Casting, the process for manufacturing cast vinyl, is much more costly than calendering. A resin is poured into a form to create an extremely thin layer on a very smooth surface. Then it goes into a curing oven.
Cast vinyl offers excellent resistance to shrinkage because it is originally poured as a liquid, rather than stretched like pizza dough; i.e. if it is not stretched, then there is no ‘memory’ for it to try to settle back into its original shape. As such, cast vinyl is usually chosen for long-term outdoor graphic applications, such as vehicle wraps.
Like calendered vinyl, cast vinyl can be produced with either a monomeric or polymeric molecular structure. It is very rare to find a monomeric cast vinyl, however, because it does not make sense to use a more ‘degenerative’ ingredient when manufacturing a more expensive product.
Colour reproduction
All four types of vinyl can accept solvent, eco-solvent, UV-curable and latex inks. That said, there will be a noticeable difference in colour reproduction between them when using solvent or eco-solvent ink sets, which permeate into the media before drying; whereas latex and UV ink sets have little effect, because they instead rest on top of the media’s surface, where they are cured.
With reference to the smaller, less uniform building blocks of monomeric vinyl compared to the larger, more uniform building blocks of polymeric vinyl, when solvent and eco-solvent inks permeate into the small, unbonded gaps in the molecular structure, it is better in terms of colour reproduction to have them as perfectly spaced as possible. So, colour reproduction becomes slightly better moving from monomeric calendered to polymeric calendered to cast vinyl.
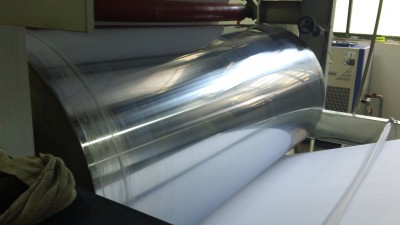
Vinyl liner
It would be ideal if the aforementioned factors were all that mattered in the production of adhesive-backed vinyls for the sign industry, but unfortunately, the chemistry is complicated and many other factors can also come into play when attempting to develop the perfect composition of print media. The vinyl’s liner, for example, is also essential in determining printing success.
As more and more manufacturers of eco-solvent wide-format inkjet printers add secondary independent printheads to their models, the average speed of printing is increasing. Indeed, the newest eco-solvent printers are nearly twice as fast as their predecessors.
When a printer is producing output twice as fast, however, it will need a heat platen twice as long to ensure the inks are fully dried before the media reaches the take-up reel. This in turn means more heat is being applied to the printed substrate, which can have a negative effect on the face stock and/or the printability of the media. Many signmakers have noticed vertical tunnelling between the pinch rollers, which is caused by rapid moisture evaporation from the liner.
For this reason, some liners are now produced with a special moisture seal, which allows them to be exposed to elevated temperatures without tunnelling the substrate.
So, in addition to finding the right vinyl for the job, signmakers also need to find the right media liner for the printer.
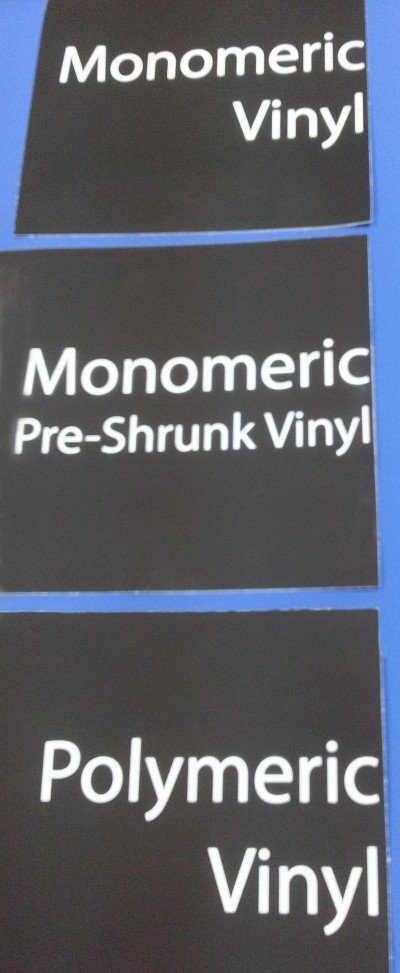
The aqueous exception
While the aforementioned ink types—including solvent, eco-solvent, UV and latex inks—are certainly popular in the sign industry, the most common types today are still traditional aqueous inks, due to their low cost and, when printed, high resolution. To accept aqueous inks, however, the vinyl requires a coating.
With the addition of a coating, concerns about unbonded molecular spaces and colour reproduction become moot. The coating ‘takes over,’ offering a very smooth surface above the vinyl’s own molecular structure.
As a consequence, any vinyl intended for aqueous inkjet printing is only as good as its coating. Most coating manufacturers, however, are not well-known to signmakers, remaining ‘behind the scenes’ of the vinyl materials that are marketed under their own brand names. So, making the right choice will be a question of comparing coatings within the context of comparing those materials.
At any rate, there is no reason to spend extra money on a coated polymeric or cast vinyl for aqueous inkjet printing. Better to find a pre-shrunk monomeric vinyl with a high-quality coating.
Matching inks to vinyls
In summary, the following considerations should be kept in mind when choosing a vinyl substrate for use with a given ink set:
UV-curable inks
These inks offer similar colour reproduction capabilities with either calendered or cast vinyl. Their useful life in outdoor applications will directly increase moving from monomeric calendered to polymeric calendered to cast vinyl.
Solvent-based and eco-solvent inks
These inks offer slightly better colour reproduction and longevity and less shrinkage moving from monomeric calendered to polymeric calendered to cast vinyl.
Latex inks
These inks will achieve similar colour reproduction with either calendered or cast vinyl. Like the afore mentioned inks, they will last slightly longer outdoors moving from monomeric calendered to polymeric calendered to cast vinyl.
Aqueous inks
The most important factor for these inks is the media’s coating, followed by the liner; the vinyl itself has very little effect on the longevity of aqueous inks. Indeed, pre-shrunk monomeric calendered vinyl is highly recommended because it is much less expensive than polymeric and cast options, yet will suffer only very minimal shrinkage over time.
E. Tyler Reich is director of product development for Qué Media, which manufactures wide-format printing media and coatings. For more information, visit www.que-media.com.