CNC Routers: Optimizing cutting and avoiding pitfalls
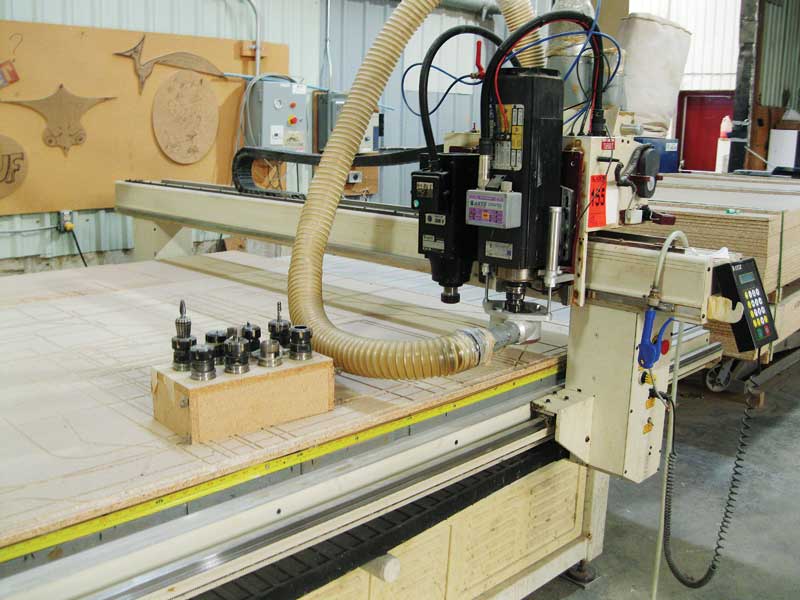
Photo courtesy TCL Asset Group
Chip load
Chip load is a measurement of the thickness of material removed by each routing edge during a cut. It is mainly dependent on the diameter of the tool; i.e. a larger-diameter tool will yield a larger chip load. The reason it matters to the feed rate formula is that a larger chip load allows for faster material removal and, thus, faster cutting.
Welding of the chip during plastic routing is reportedly one of the industry’s most irritating problems, as it can be costly in time and scrap rate, yet is entirely avoidable. Common reasons include improper chip load, small-diameter tooling and improper direction of cut. The key to plastic routing, then, is to produce the right size of chip to prevent the level of heat that can cause welding.
Further, chip load heavily affects the surface finish of plastic. This is an important consideration for plastic signs, exhibits and point-of-purchase (POP) displays that are constantly in public view. Using the proper size of chip will eliminate excessive knife marks in soft plastics and a cratered finish in hard plastics.
Flutes
A flute is a groove that wraps around the tool where the chips are released from the cutting edge. The larger the number of flutes, the faster the material can be cut. A two-flute router bit will cut twice as fast as a single-flute bit, for example, and a four-flute bit will cut twice as fast as the two-flute bit.
That said, it is important to take into account the rate at which a bit will break. As cutting speed is increased with a higher number of flutes, the structural integrity of the bit is reduced. All flutes dull at the same pace, but since a four-flute bit has less structural integrity than a two-flute bit, it will not last as long and will break at a faster rate.
For that reason, one- and two-flute bits are recommended for general use and three- and four-flute bits only sparingly. The trade-off of increased speed for lower structural integrity is simply not worth it, as when tools break more frequently, the overall costs of consumables rise noticeably.
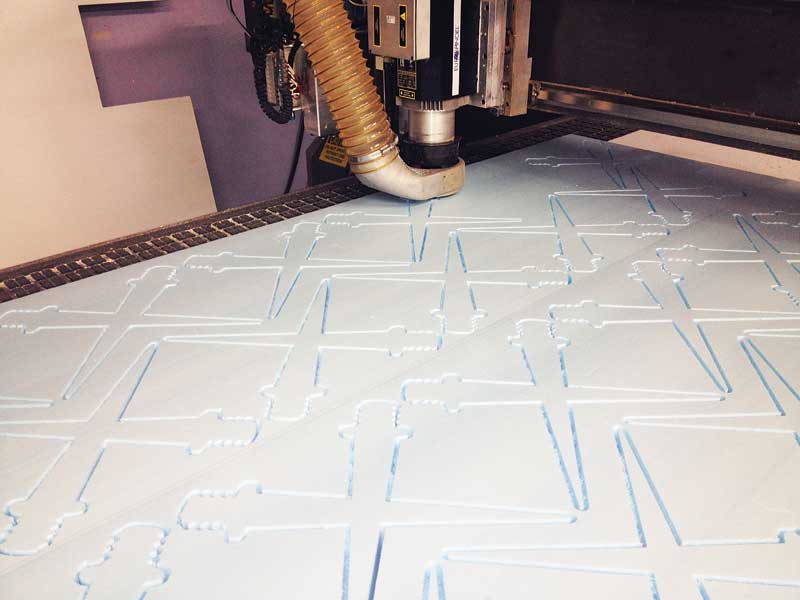
Photos courtesy TCL Asset Group
Tooling
With the aforementioned variables defined, it becomes much clearer how to use different inputs with various materials to optimize a CNC router’s feed rate without sacrificing the finish. The next step is to make the right tooling choice.
Proper tooling selection is crucial to achieving optimal results in routing. Many CNC machine operators assume determining cutting edge quality is merely a matter of choosing the most appropriate tooling dimensions. This is not the case, unfortunately, as selection comprises a far more complex set of factors.
The single most important aspect that can significantly affect edge quality is whether an ‘upcut’ or ‘downcut’ tool is used for the job. The difference between these tools is the direction of the router bits’ flutes—and the choice between them will depend on (a) the type of material being cut, (b) the thickness of the material and (c) the nature of the required finish.